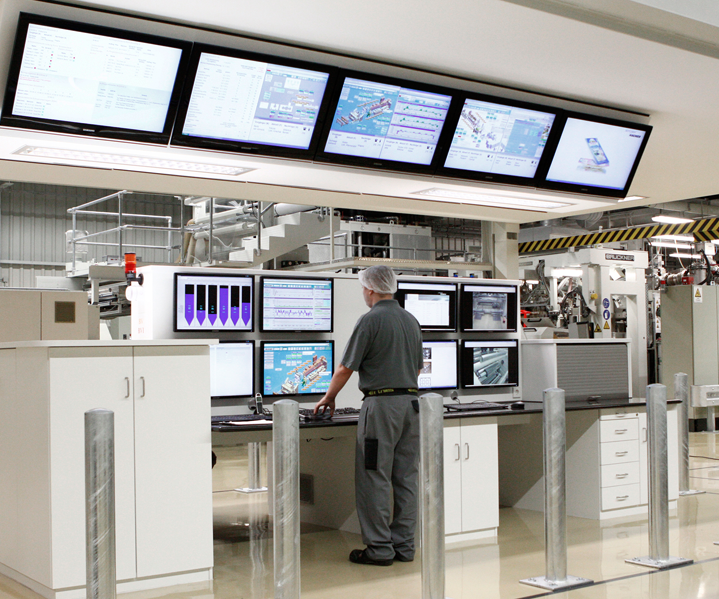
Starting with the feed, dosage, extrusion parameters up to the confectioning, he is able to control and monitor all processes. At the same time, the systems offer him essential decision support by means of optical and acoustical signals as well as interactive messages.
On account of the dimension of the installation, this information is available in different places of location within his area of responsibility as well as centrally for the management. The data for the film specification referring to the order are made available centrally via the SAP system. Any information accompanying the product is at the machine operator’s disposal continuously and is permanently updated. The manufacturing parameters and data are permanently recorded and archived in the Roll Data History System (RDH) and the optical web inspection system.